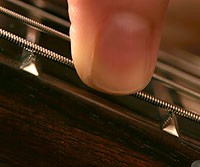
The Petillo Precision Fret™
U.S. Patent No. 4,064,779
Why a Petillo Refretting?
To answer this question, we must first examine a conventional refretting. We ask some very important questions. Remember that the heart of the instrument is the frets and the fingerboard, and if the positioning of the slots is not true to the fingerboard scale then the instrument will play out of tune.
- Why should there be a refretting?
- What method is used to remove the old frets?
- Is the fingerboard damaged when frets are removed, including bindings?
- Are the fingerboard fret slots damaged or have they become too wide to hold the frets into the fingerboard?
- What process is done to remove twists, humps, or wear throughout the fingerboard?
- Are the inlays damaged, destroyed, removed, etc?
- How are the frets finished off?
- Is the action low without buzzes or dead spots?
- Do the installers guarantee that your instrument will play in perfect tune?
- Will every note be in tune with each corresponding note anywhere on the fingerboard?
- What experience do the people have who repair your instrument?
- Are they competent?
- Is the work done in a professional manner in a reasonable length of time?
These are just a few questions you should ask before considering a refretting on any of your instruments. In my 39 years of making, repairing and altering stringed instruments. I have seen thousands of instruments that were altered so badly, without skill or consideration, that they cost 3 to 4 times more than the original price to restore the instrument back into working condition. A conventional refretting is removing the old frets and hammering or pressing in new frets. The problem with this method is the frets are held in place by the friction of the wood in the fingerboard alone. Due to climatic changes, improper storage, perspiration from playing that corrodes the fret alloy making it weaker, cleaning oils that soften the wood, and poor removal of the old frets (which widen the fingerboard slots affects the friction join), many problems result: high frets, buzzes, dead spots, intonation difficulties, and the edges of the frets rising off the fingerboard (sometimes causing the high “E” string to get caught underneath the frets after bending or strumming).
The Petillo Precision Fret™ (Fig. 1, left) allows the strings to rest in the center of the fingerboard slot; in this position the strings are perfectly centered in the middle of the fret, resulting in perfect intonation. The conventional fret (Fig. 1, right) has a flat top which causes the strings to rest in a wide flat area with no accurate string placement, thus causing intonation difficulties. The four categories below – Fret Repositioning, Fingerboard Radius, Fret Alloy, and Micro polishing, describe the preparation and process of a Petillo refretting.
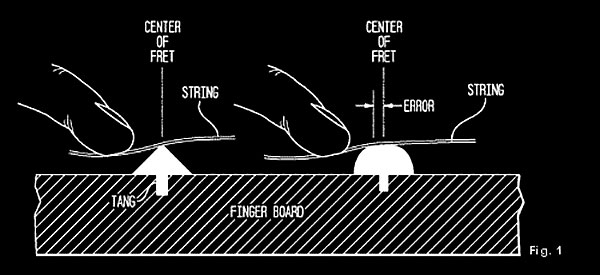
Fret Repositioning
In many cases the fret slots which hold the frets into the fingerboard are sawn in the wrong places. Before sawing new slots we make sure that the fingerboard slot positioning is located properly within the particular fingerboard scale. If repositioning is needed new slots are plugged with the same wood species of the fingerboard, then resawn to tolerance of .002 of an inch. Once properly resawn to the correct slot positioning of fingerboard scale then the Petillo frets are ready to be installed. A lot of intonation problems come not only from the flattened-down tops of a conventional fret, but also from inaccurate division of the fingerboard scale.
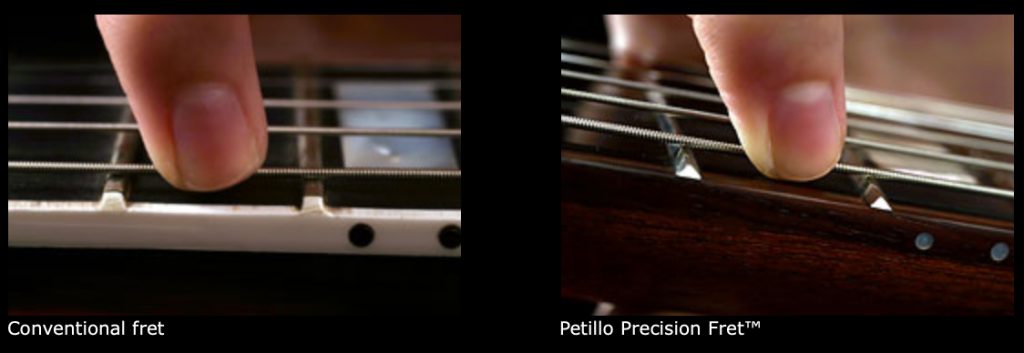
Conventional fret Petillo Precision Fret™
Fingerboard Radius
Sometimes if necessary, the radius of the fingerboard is altered to fit the players hand and style, or to remove twists, humps, and wear in the fingerboard. The flatter the radius of the fingerboard the lower the action can be. To accomplish this the fingerboard is planed, scraped, and sanded to a new radius. The inlays will still be intact. Changing the fingerboard radius is optional. If the musician desires to keep the original radius then the fingerboard is just clean sanded true. Many players find that by changing the radius, they discover an optional lower action, and greater ease in bending strings, playing chords, and overall string movement.
Fret Alloy
Most frets used in manufacturing and sold from repair catalogs are made from a soft nickel tin alloy with flattened-down tops. Because the alloy is made of a soft metal, its life span is short with expected wear. The main concern with choosing the right material is not only to make the life span of the frets endure years of playing, but also to improve tone, volume, and sustain with perfect intonation throughout the fingerboard. Over the years, I have experimented with different exotic metals for frets, such as Titanium, Stainless Steel, Hestelloy C-22, Inconel 718, Ceramic coated material, Zirconium Tungsten Coatings, and Cobalt Based Super-Alloys. In the end, the best of these materials proved to be a Stainless-Steel alloy. This material proved to be the most effective in achieving my objectives for superior fret performance.
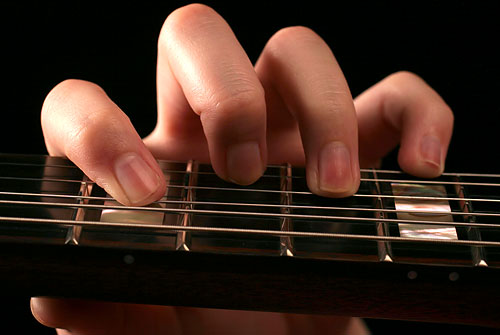
Modified Gibson Les Paul, serial#: 030551
Modifications: Nigerian Ebony fingerboard with Abolone block inlays, outlined with Rosewood binding.
Micro Polished Petillo Precision Frets™ and fingerboard with Petillo size .009 strings.
Micro Polishing
To micro polish is to produce a finish on a surface of an object, making it as smooth as possible, so that there are no scratches or imperfections, only a smooth high-gloss surface. The molecular structure of the Petillo fret alloy is changed after micro polishing with a specialized coating process which makes the surface area of the fret harder. Each fret is done individually. What value does this have for fretted instruments? How many times have you played a guitar, bass, or any fretted instrument where the strings seem to be restricted by rough frets, or when bending the strings makes a rasping noise? Once the micro polishing of the frets is completed, effortless string bending and finger positioning, which give longer life to the strings and fret alloy, results. To assure the longevity of the frets, the fingerboard is then buffed with Petillo Fingerboard Dressing, sealing the wood from finger oils, perspiration, and moisture. This compound is specially designed for dark unfinished woods such as Ebony, Rosewood, Walnut, Tulip Wood, etc.
This fret micro polishing and fingerboard buffing process can be applied to conventional frets, making a vast improvement in the performance of your instrument. However, it will not match the playability achieved with The Petillo Precision Fret™.